Brooke Fisher
Photos by Mark Stone / University of Washington
September 25, 2020
Professor Jeffrey Berman in front of the composite beam specimen on the first day of testing.
On-campus research activities may have been limited this summer due to COVID-19, but in CEE’s Structural Research Laboratory engineers continued to make progress on critical research, such as testing a new sustainable flooring system that will be used for the first time on UW’s campus.
“We’ve been continuing to work on the tests through all of the shutdowns because construction can’t continue without the tests being done,” says CEE professor Jeffrey Berman. “This is a critical path activity for what is being designated by UW as a critical project— the health sciences building will support medical research within the university.”
In early summer, CEE researchers assisted engineers from KPFF Consulting Engineers with the commercial testing of a new cross-laminated timber (CLT) flooring system, which will be used in the UW Health Sciences Education Building (HSEB), for which a groundbreaking was held in August. The HSEB will be one of two newly constructed buildings on UW’s campus to utilize the new structural system.
“The UW really pushed and wanted to go in this direction for lowering the carbon footprint of new facilities,” says Berman. “This is all about sustainability and reducing production of CO2 in building construction, which is very harmful environmentally. By using timber floor systems, there is a potential significant benefit of reducing the climate change impacts of building construction.”
In the construction industry, concrete is one of the most widely used materials. The main ingredient in concrete, cement is responsible for about 8% of global CO2 emissions, according to a Chatham House study. The CO2 is produced from both the chemical process and burning of fuel required to make cement. Although the new CLT flooring system utilizes much less cement, it has been slow to gain adoption in the United States.
“We are working with clients to try to popularize CLT and make it a viable and competitive structural system,” says Addie Lederman, structural design engineer with KPFF. “CLT has gained traction because it is more sustainable than traditional building materials.”
A sustainable timber product, the lumber used for CLT panels comes from managed forests that are sustainably harvested, rather than cutting down old growth. Comprised of multiple layers of lumber stacked in alternating directions, CLT flooring systems also utilize less-desirable pieces of wood, such as timber with a small diameter.
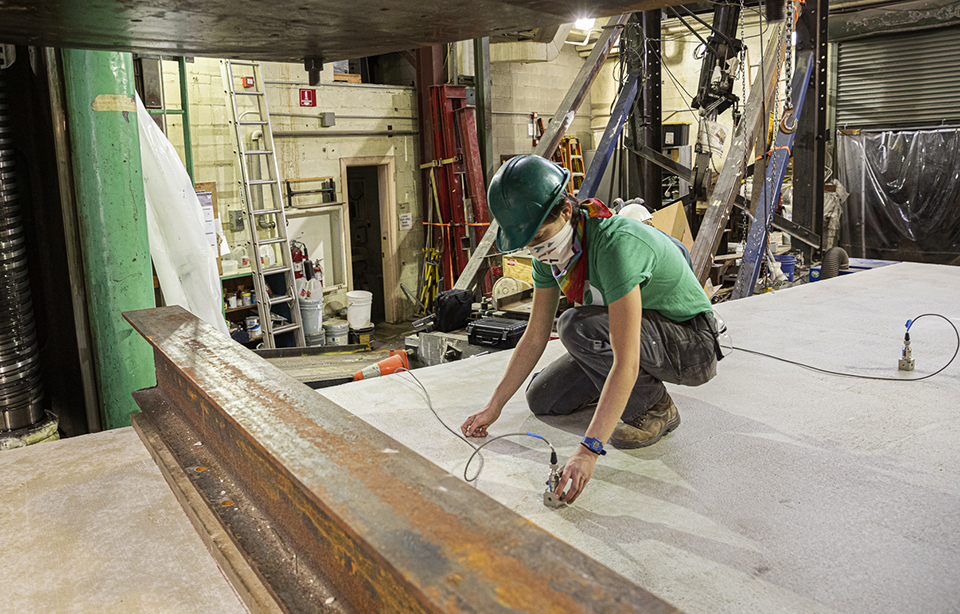
Placing accelerometers on the composite beam specimen in preparation for taking vibration measurements on test day.

KPFF structural design engineer Addie Lederman takes vibration measurements of the composite beam specimen on test day.
With funding from a grant from the U.S. Forest Service, KPFF engineers are developing guidelines for designing and implementing CLT flooring systems for vibration performance. Since the CLT flooring system that will be used in the HSEB is a new type of composite steel and concrete system, the engineers conducted two rounds of testing in CEE’s Structural Research Laboratory in order to obtain building permits. Using a Universal Testing Machine called “Big Baldwin,” they tested the flexural strength of 30-foot long steel beams overlaid with a CLT floor slab and a small amount of concrete.
“This is a new, innovative structural system that does not have prescriptive requirements in the current code,” says Jessica Westermeyer, KPFF project manager. “For new systems like ours, the International Building Code allows specimens to be tested to show compliance. The specimen was loaded to 200% of the design load, and that load was held for a full 24 hours. The code then requires 75% of the imposed deformation to be recovered, and then the specimen is loaded to 250% of the design load or more.”
To estimate the total reduction in global warming potential of the HSEB, the project architect, Miller Hull, is currently working on a full lifecycle assessment of the building, which will take into account the new CLT flooring system.
“We are very optimistic [about the study] as CLT panels are made from 100% sustainably harvested timber. In addition, timber is the only major building material that is both renewable and naturally sequesters carbon by removing CO2 from the air while trees grow,” says Westermeyer.
KPFF structural design engineer Addie Lederman stands on the composite beam specimen platen before the concrete topping is poured.
This research is funded by a grant from the U.S. Forest Service.